From Energy Meter to ERP: Integrated Energy Management
Measuring and counting checklist for small and mid-sized enterprises
In times where it's difficult to calculate energy prices, continuous energy management has become a crucial economic factor. The prerequisite for this is that the ERP software is designed for this purpose. As one of the leading providers of ERP+ software solutions for the mid-market manufacturing industry, we have therefore added the solution of our group company ENIT to our portfolio. And we know what is important when it comes to measuring and counting, especially for small and mid-sized enterprises.
The path to integrated energy management
- Choose the right meter
Analog meters are not suitable for continuous energy management. Instead, economic reasons should prompt you to choose multifunction meters that feature communication interfaces. They collect all relevant data and allow you to read not only counters but also current values. Suitable interfaces make them compatible with further data collection systems. By contrast, power quality analyzers are much more expensive and don't offer any added value in most use cases. - Pay attention to the communication protocol
For the integration into the IT landscape and especially the ERP system, the meters must support a standardized communication protocol. You should steer clear of proprietary protocols from individual providers that are not compatible with other solutions. The protocol Modbus TCP has turned out to be a good choice. It facilitates the implementation of an energy management system. - Check for compliance with the calibration regulations
Under certain circumstances, for example, when surcharge-privileged amounts of electricity are transferred to third parties, authorities demand that the measure be in compliance with the calibration regulations. Unfortunately, the definition of the calibration regulations for a measuring device differs between states. If you are required to measure based on these criteria, you should consult the measuring and calibration authorities responsible about your specific requirements. We recommend not to take this matter lightly since irregularities are classified as administrative offense and punished with heavy fines. In general, a corresponding measuring device consists of a plug-in current transformer – no split-core current transformer – assessed for compliance and a Measuring Instruments Directive (MID) current meter. The compliance of the current transformer has to be reevaluated after eight years. - Use the transfer meter as an information source
By installing unnecessary or wrong meters, you send up the costs for the energy management system. In a first step, it's enough to measure at the transfer meter and the main distributions. After a data-based analysis, you might have to include plants as well. The transfer meter is relevant to energy management as it measures the energy supplied by the power grid. Besides entering the 15-minute load curve as basic information, it also enters further comprehensive parameters and helps to uncover cost drivers, for example with regard to
Load peaks,
Standby consumption,
Voltage fluctuations
Or power asymmetries.
Before entering into submetering (see Figure 1), you can analyze at this point whether there is any potential for savings at all.
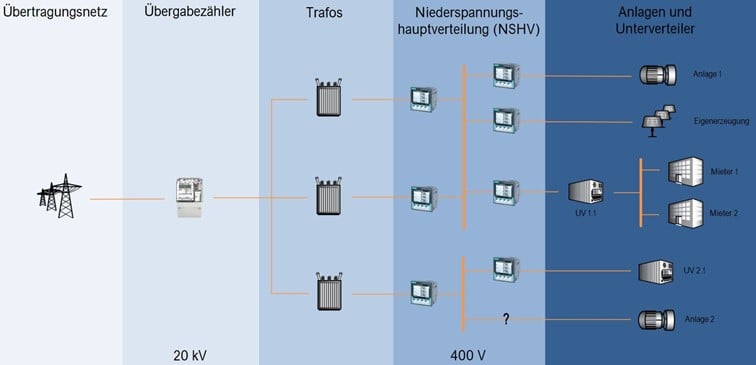
- Approach submetering strategically
The transfer meter is followed by the 20kV distribution with the transformers that supply the busbars of the low-voltage main distribution boards (LVMDB). They usually have measuring devices affixed. We also recommend universal measuring devices here since you can easily reconnect older indicators to them. They fit the common control cabinets, which is also a strategic measuring point as the cables are easily accessible and you don't need any further cabling for communication lines. Measuring in the subdistribution board or directly at the plant is much more costly. However, universal measuring devices have to be connected to the ERP system via the energy management solution if there is an unmeasured rest that cannot be explained by an energy flow chart. In this case, you have to conduct detailed measurements in order to trace the energy loss.
Energy management with the ERP system
Professional sustainability management helps you to register, control and document the energy demand and carbon footprint across the company, be it in finance, sales, purchasing, production or service.
With the integration of energy management solutions – the group company ENIT in case of proALPHA –, the ERP system serves as a data hub for monitoring and controlling all energy flows and displaying consumptions and emissions transparently. As the single source of truth, an ERP system that is supplemented with energy management and carbon tracking components creates the basis for suppliers to becoming carbon neutral. It contains all data for the CCF and PCF, provided that they have been entered, and also enables you to develop reduction strategies, take relevant actions and monitor the development of emissions.